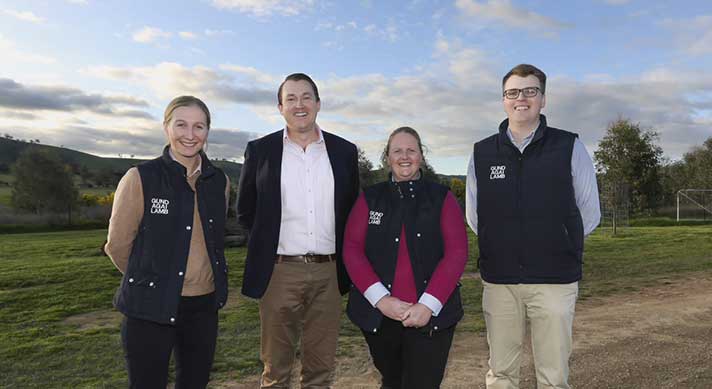
Processors play an important role in the integrity system. While livestock producers are responsible for keeping their integrity records in order and ensuring their on-farm practices align with integrity system requirements, processors must ensure that livestock consigned for processing are fit for consumption.
The Australian red meat integrity system combines livestock traceability with on-farm assurance to maintain the integrity and reputation of Australian red meat. This system underpins our livestock selling system and delivers customer confidence in the red meat products we produce.
Integrity Systems Company (ISC) is responsible for managing and delivering the core elements which make up Australia’s red meat integrity system.
Australian processors require producers to be LPA-accredited to be able to purchase their livestock.
The current LPA National Vendor Declaration (LPA NVD) is required for all livestock movements, including property to property, through saleyards, direct to processors and to feedlots, and to the live export trade.
Processors must record information on the database to comply with state regulations relating to biosecurity and traceability.
Digital consignments the using eNVD web-based system and the mobile app provide benefits and savings for processors including:
Access this page to find out more about the LPA program and find out how to help your clients meet their LPA requirements, create farm records and LPA NVDs.
NLIS is Australia’s system for the identification and traceability of cattle, sheep and goats. NLIS reflects Australia’s commitment to biosecurity and food safety and provides a competitive advantage in a global market.
When livestock are physically moved, a transfer must be completed on the NLIS database. This means the animal’s NLIS device number is transferred from one PIC to another PIC to reflect its physical location.
There are two types of transfer – movements of animals which are identified individually with RFID electronic eartags. This is for sheep and goats in Victoria and all cattle across Australia. The second is mob-based movements for sheep or goats which have a visual tag. Sheep and goats in all states, except Victoria, can complete both types of transfer depending on the type of tags they use on-farm.
All processors must record information on the database to comply with state regulations relating to biosecurity and traceability.
Post-sale summaries are a legal requirement of the selling agent and, as a processor, you must receive this before midnight on the sale day. A post-sale summary provided by a selling agent to the operator of an abattoir must include:
myMLA is the gateway to accessing a range of MLA products and services including LPA. It provides a single sign-on facility to your NLIS, LPA, MSA and LDL accounts – which means you only need to remember one username and password. View the step-by-step PDF guide or short video to learn how to link your accounts to myMLA.
When selling livestock, always check the ERP status of the PIC the livestock are from by running the ERP PIC status report.
If a PIC status is identified it is vital this is captured on an NVD so the information can be transferred to the receiver. This is so they know what they have bought in a consignment and can it manage accordingly.
Producers can use LDL to understand why their consignment did or did not comply with market requirements, including carcase compliance and animal health issues.
Processors have customised grids based on individual market requiremens, so producers can easily see if a carcase was downgraded (i.e. discounted) and the reason why. Producers can access solutions to address non-compliance issues to help them decide what changes to make to increase compliance, and ultimately their returns.
Producers can also compare their own carcase performance figures to industry benchmarks within their region, state or the whole country, to identify further areas of improvement.
The Australian red meat industry produces and collects a wide range of data at various points along the livestock supply chain. The LDL program provides a solution to enable greater utilisation of this information by presenting feedback in a user-friendly format that can aid in decision-making throughout the supply chain. Accessing this information improves the bottom line for producers and red meat processors.
Animal diseases and defects affect meat, offal and sometimes the carcase, causing these products to be condemned. MLA research indicates meat and offal condemns cost the beef processing sector up to $50m per year. Similarly, research into small stock shows that $110 million is lost annually through 10 common conditions found during processing. It is also estimated that on-farm sectors bears 86% of the cost.
LDL includes data from the National Sheep Health Monitoring Project (NSHMP) and Enhanced Abattoir Surveillance (EAS) Program, which allows sheep producers consigning to participating abattoirs to access their inspection results against 19 disease and defect conditions. Some beef producers can also access disease and defect feedback from data uploaded to LDL by participating companies. In the future, sheep producers will be able to access individual disease and defect data as a couple of plants are working towards this.
Contact ISC Customer Service for more help with integrity at info@integritysystems.com.au or on 1800 683 111 between 8am and 7pm (AEDT), Monday to Friday.
Be sure to sign up to ISC’s monthly newsletter, Integrity Matters, for practical help and information on LPA, NLIS, NVDs and more. You can also follow ISC’s Twitter account and Facebook page for additional news and updates on integrity, or visit ISC’s Tools and Resources page to access a large range of practical tools and how-to guides to provide further assistance with integrity programs.